The philosophy of dematerialisation
Valcucine was the first company in the world to fully make over the parts that constitute the structure of a kitchen – the door, top and carcass – achieving cutting-edge solutions
that are a perfect synthesis of beauty, formal simplicity and technical intelligence.
These parts have been renewed by respecting the principle of dematerialisation that implies using less raw materials and less energy with a view to eco-sustainability which has
always been at the basis of Valcucine’s design philosophy. Without compromising on their solidity, partially or fully recyclable structures are broken down to the essentials. This describes how products that actually improve functions, aesthetics and the environment and that have been patented all over the world are born.
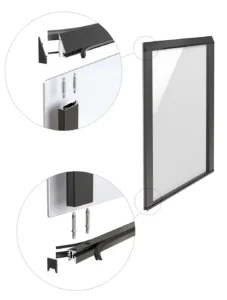
The door
The Valcucine door is made up of an anodised aluminium structural frame featuring only mechanical joints and of a decorative panel welded to the frame in such a way as to be invisible from the outside. This technologydelivers a more functional and higher-quality door that pairs solidity with lightness and is a real novelty in the industry.
The variety of materials, colours and finishes available for the decorative panel expresses the product’s flexibility and offers a tailored approach to the project. The result is a revolutionary door, covered by an invention patent and favouring brand new aesthetic solutions that can evolve and follow variations in tastes over time.
The top
The Valcucine top consists of an anodised aluminium structural frame and of a worktop available in a wide range of finishes. The structural frame makes the top sturdy and light while using less material compared to traditional tops. With a view to optimising natural resources, some structural parts are made from secondary aluminium. Reducing the thickness of the top, which consequently makes it lighter, offers advantages in terms of transport and installation as well.
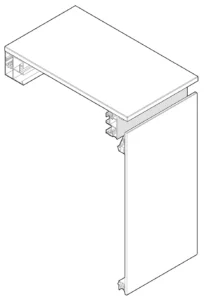
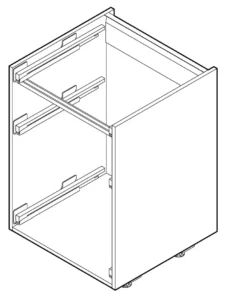
The carcasses
Melamine-faced chipboard carcass
This carcass is made of chipboard coated with sheets of melamine paper that offer good resistance to scratches, abrasions and stains. The chipboard core used by Valcucine offers greater water resistance than the types normally found on the market and is P3 rated. The carcass complies with the American TSCA Title VI certification and with the limit values set by the strictest regulations in the world on formaldehyde emissions, i.e. the Japanese F**** standard.
Plywood carcass
This carcass is made of layers of wood joined together using adhesives and is covered on both sides with sheets of thick HPL that give the panel excellent scratch, stain, abrasion, impact, steam and heat resistance. Our plywood is more water resistant than grade P3 chipboard. It is particularly suitable for countries with a high rate of humidity.
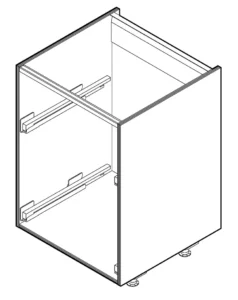
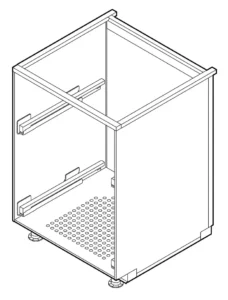
Aluminium or glass Invitrum carcass
This carcass features honeycomb aluminium or glass side panels with a glass bottom panel and aluminium connecting elements. It is completely devoid of glues and can be dismantled and recycled. Whereas traditional carcasses, since they are fitted side-by-side, feature two side panels where they are united, to optimise the use of raw materials Invitrum has been designed to have a single, 10-mm thick side panel.